DOWNLOADS
Open interactive popup Article (8 pages)Industries such as chemicals, metals and mining, oil and gas, and power generation typically require computerized, near-real-time process controls. These basic control systems are often operated manually to adjust for desired target values (known as “set points”) in response to changing conditions, such as temperature, pressure, or incoming feedback. However, nuanced advanced-process-control (APC) systems often result in significantly better performance by automating responses—similar to how cruise control on a car regulates speed and maximizes fuel efficiency.
About the authors
In recent years, industrial companies have made significant infrastructure investments in APCs but have extracted only a small fraction of their value. In some cases, less than 10 percent of installed APCs are activated or optimized, while others have not been reevaluated to ensure inputs and constraints are properly tuned and solving for the right objective. And those companies that do tune their APCs sometimes fail to sufficiently test them, or they lack adequate management systems to track and report performance and rely on external vendors for maintenance.
MOST POPULAR INSIGHTS
Enabling APCs to operate more efficiently requires a combination of regular tunings and a comprehensive approach that addresses sensors, devices, and control loops, as well as educating and training control-room operators on the latest techniques. With the recent advances in computing power (and lower computing costs), APCs can be tuned using machine-learning models, and advanced analytics can produce responsive insights from large amounts of historical data, increasing the speed of the tuning process and reducing human bias or intervention.
Chief information, technical, and operations officers who take the necessary steps to optimize their APCs in a repeatable, systematic manner can help realize significant gains—including an up to 15 percent increase in throughput, a 5 percent increase in yield, and a 10 percent reduction in energy consumption. In fact, our research shows that optimizing APCs at processing sites can generate $15 billion to $27 billion globally.
How advanced process controls work
The way organizations utilize control logic can be visualized as a pyramid. APCs sit near the top, executing set points with base-layer controllers (BLCs) such as programmable logic controllers or distributed control systems (Exhibit 1). In this sense, APCs facilitate communication between system-level controls, subsystems (sensors and instruments), and equipment (the actual machinery).
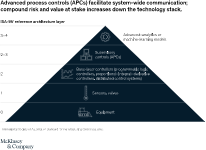
In the mining industry, for example, APCs communicate with different feed sources to deliver the target particle mix to a mill1 to be processed (Exhibit 2). They also help ensure an optimal retention time by controlling the feed rate of ore and water (otherwise known as “ore hardness”). Each real-time controller drives a single controlled variable to a prescribed set point. For instance, one controller might adjust the speed of the dilution pump to maintain the desired water flow, which informs the APC assigned to retention time.
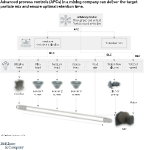
APCs are only as good as the set-point targets and constraints inputted by operators and the quality of measured process variable data (see sidebar, “The three types of advanced process controls”). Yet, many companies have neglected reviewing their set points for years.
The three types of advanced process controls
Others simply don’t have the required in-house capabilities to maintain their APCs and are therefore dependent on vendors. Managing these relationships requires clearly defined strategies, and companies that already struggle with optimization are sometimes left in the dark. Relying solely on an already-lacking, in-house maintenance strategy for underlying control loops, equipment, and sensors will inevitably result in less-than-ideal APC performance.
Those that do have the capabilities to maintain their equipment may still lack the discipline to keep APCs activated and in good health. As an example, some operators prefer to manually run processes, given their distrust in APC performance, which is further aggravated by a lack of management systems that track or rate performance.
CIOs, CTOs, and COOs responsible for optimizing their organizations’ technologies should closely examine how to use advanced analytics to generate maximum value from APCs.
How to maximize value from advanced process controls
CIOs, CTOs, and COOs responsible for optimizing their organizations’ technologies should closely examine how advanced analytics can be used to generate maximum value from APCs. Doing so requires a comprehensive approach that addresses challenges across three categories: people, processes, and technologies.
- People. Improve the utilization of APCs through better performance management of operators and vendors and take a comprehensive change management approach.
- Processes. Improve underlying layers of APCs with better processes to maintain the health of sensors, instrumentation, and BLCs.
- Technologies. Improve APC design and logic by identifying the right objective function and input–output relationships, reviewing the constraints, and employing advanced-analytics models.
The following examples illustrate how APCs can be optimized along these categories.
Example 1: Basic-materials company
A North American company that relies on a smelter experienced high variability in slag temperature as a result of poor controls.2 This irregularity was risky, as dipping below the threshold temperature could freeze the slag and halt operations. In response, operators set overly conservative temperature limits, compromising thermal energy that could otherwise be used to improve furnace efficiency (Exhibit 3). And satisfying a combination of multiple process constraints, including steam flow and the oxygen-to-carbon ratio, further complicated matters.
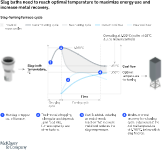
The company reviewed its process control systems through a comprehensive approach.
- People. Metallurgists and operators were engaged to ensure that each APC was solving for the right objective function throughout the optimization process. And APC-performance dashboards were created for plant leadership to ensure accountability and sustained improvement in APC utilization.
- Processes. A review of the underlying BLCs, sensors, instrumentation, and maintenance records led to a focus on calibrating sensors and coal-flow controllers. Risk assessment and change-management efforts around control engineers, metallurgists, and operators also complemented this review.
- Technologies. Control engineers built predictive models for each output, applying historical data from more than ten million data points collected over the course of two years. A subsequent optimization algorithm found the best-possible model parameters, thereby improving the logic of the APCs.
As a result of this approach, the company increased zinc recovery from the fumer by around 8 percent.
Example 2: Pulp-and-paper mill
Despite investing in state-of-the-art equipment and APCs, a large North American pulp-and-paper mill was suffering heavy operating losses. Its output was well below industry averages, and poor fiber quality caused downstream issues in paper and tissue finishing lines.
A review revealed that most operators had little faith in the mill’s critical APCs and chose instead to run the mill manually. Several APCs had never been properly set up in the first place, and there was no process to monitor and maintain control loop health. At the instrumentation layer, critical sensors had never been calibrated, effectively rendering certain APCs useless.
- People. Mill leadership set clear expectations with control-room operators regarding APC use and invested in change management to ensure sustainability. These efforts included implementing visual dashboards and daily shift huddles around APC use, as well as operator education about the functions of the APCs.
- Processes. The mill focused on vendor management, employing a program to prepare and calibrate idle APCs to deliver guaranteed performance. This program included identifying instruments that needed to be commissioned or calibrated and holding vendors accountable for testing and monitoring.
- Technologies. The company applied advanced-analytics models to provide better set-point recommendations and to optimize total mill profit per hour. This ultimately resulted in new targets and centerlines (upper and lower tolerances) for various steps in the process, such as digesting, oxygen delignification, and bleaching.
After 12 weeks, the APC transformation led to $21 million in earnings before interest, taxes, depreciation, and amortization, increasing throughput by 15 percent and yield by 4 percent (Exhibit 4).
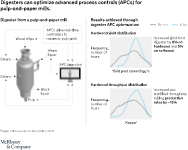
Companies interested in extracting more value from suboptimized APCs should look for any of the following indicators:
- a high degree of variability in critical process indicators, including throughput and recovery
- a low utilization rate (less than 80 percent) of existing APCs that control key processes
- no process to periodically (at least once a year) review APC logic or set points
- no rigorous management system to track the health of underlying BLCs, instrumentation,and sensors
If any of the above conditions are observed, there is likely significant opportunity to unlock additional value through APC optimization. Collaborating with APC vendors to identify, calibrate, and tune the crucial underlying BLCs and sensors can be an initial no-regrets move. Further optimization initiatives should be prioritized based on impact and feasibility. With a comprehensive approach based on advanced analytics, companies can now optimize their APCs in a repeatable, time-efficient, and systematic manner, capturing significant improvements in throughput, recovery, and energy savings.